RODEO, un succès dans le perçage orbital robotisé pour l’aéronautique
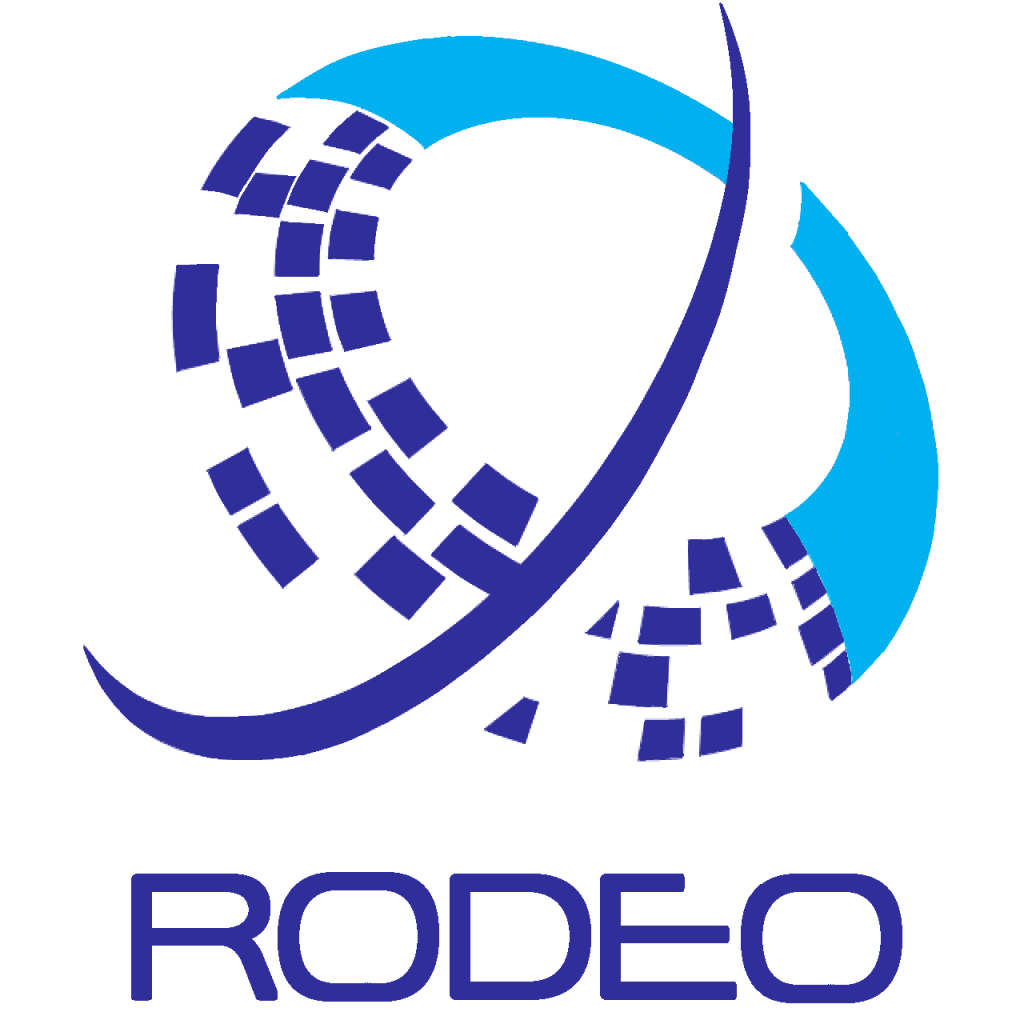
Le projet européen RODEO (Robotized Orbital Drilling Equipment and Optimized residual stresses ou équipement de perçage orbital robotisé et contraintes résiduelles optimisées), porté par la société PRECISE FRANCE, a été labellisé par le Pôle EMC2 le 14 mai 2016 et financé la même année par le programme européen H2020 CleanSky2. Il s’inscrit dans l’un des 4 domaines d’activité stratégique de la feuille de route du Pôle, celui de la “Performance Industrielle”. En février 2017, le kick-off du projet marque le début d’un long travail de recherche et d’optimisation qui aura duré 3 ans pour se terminer le 31 janvier 2020 avec un budget global de 500 000 €.
5 partenaires composent le consortium :
- PRECISE France, le porteur du projet, est concepteur de solutions de perçage orbital et expert en broches d’usinage également adhérent du Pôle EMC2 depuis 2008 – l’outil coupant spécifique breveté par PRECISE France a été réalisé par HAM FRANCE. Ces deux sociétés font partie du groupe PRACARTIS ;
- Le laboratoire LS2N, orienté procédés de fabrication smart machining (usinage fabrication intelligente) et robotique, rattaché à l’Université de Nantes, adhérente EMC2 depuis 2005 ;
- MITIS, expert en technologies et procédés de perçage, adhérent EMC2 depuis 2012 ;
- L’Institut Clément Ader, rattaché à l’Université Toulouse III Paul Sabatier ;
- KUKA System Aerospace, intégrateur robotique.
De l’objectif au succès du projet
RODEO avait pour but de concevoir un équipement de perçage orbital robotisé léger avec des outils de coupe et des conditions de fonctionnement appropriées pour permettre le perçage de trous de petit diamètre et étroitement espacés dans de l’aluminium avec un contrôle précis des contraintes résiduelles induites.
Alain Auffret, Directeur technique chez PRECISE France, également adhérent au Pôle CIMES et Président du Club Hydrogène, détaille :
“Le demandeur de la plate-forme européenne était SAAB en Suède. Sa demande était de réaliser l’assemblage de portes d’avion, pour Airbus principalement, avec un système innovant sur des robots légers. On a dû développer une tête orbitale, de façon à réduire les efforts de coupe par rapport au perçage. On a donc développé un orbital spécifique, mais aussi un outil coupant associé, qui a la fonction de galetage. Autrement dit, il peut changer la dureté lorsque l’on perce. Ce qui représente un avantage énorme au niveau de l’assemblage lorsque l’on vient mettre un rivet dans le trou par la suite.”
Les résultats sont un succès : les travaux de modélisation 2D et 3D sur les contraintes résiduelles induites par une opération de perçage ont été réalisés et permettent de mieux comprendre et maîtriser ce phénomène.
Une tête de perçage orbital compacte et légère a été conçue et entièrement testée. Ses performances et son poids très léger permettent d’envisager son utilisation au bout d’un bras robotisé. L’adaptation de la tête de perçage sur les bras robotiques de KUKA a été étudiée dynamiquement, afin de définir et d’optimiser les phénomènes de rigidité et de résistance aux vibrations. Le bras IIWA s’est finalement révélé manquer de rigidité pour l’application prévue, mais le bras KR60 s’est avéré être parfaitement adapté.
L’outil de perçage et la tête de perçage ont été associés avec succès à un bras robotique pour constituer un système de perçage orbital robotisé validé, léger et compact, capable d’effectuer les travaux attendus.
Alain Auffret complète :
“Le nouvel effecteur est très compact et fait moins de 10 kg avec son axe de perçage. Pour la V2, la version aboutie, la vitesse du mouvement orbital va être réglable de 500 à 2000 tours, et la vitesse de rotation de l’outil coupant va être réglable de 10 000 à 50 000 tours. L’effecteur a son propre axe de perçage, un axe Z, qu’on appelle aussi axe W, qui va permettre au robot de se positionner pour, ensuite, effectuer le perçage.”
PRECISE France a recruté Jacques Prono, un consultant nantais bien connu des adhérents du Pôle EMC2, gérant du Cabinet DISTINGO CONSEIL, pour assurer le pilotage et le reporting de ce projet européen. Il précise :
« Les appels à projets Cleansky offrent des opportunités très intéressantes : le besoin industriel est précis et détaillé et sur les topics RIA (Research and Innovation Action), on peut répondre en solo ou en petit consortium, avec un financement record de 100% du budget. Tous les partenaires de ce projet RODEO étaient français et habitués à travailler ensemble. Le montage a donc été facile. Attention toutefois, la sélection est européenne et il faut vraiment présenter une expertise pointue et reconnue, parfaitement en ligne avec les compétences souhaitées. Par ailleurs, il est indispensable d’accorder une fraction suffisante du budget aux actions de reporting et de dissémination, d’autant plus que le budget global est réduit. »
L’intervention de MITIS pour garantir le niveau de contraintes résiduelles
MITIS a été invité à participer à ce projet en tant qu’expert sur la mise en œuvre et le développement de procédés. Cosme de Castelbajac, Chargé d’Affaires pour MITIS :
“Par rapport au procédé classique de perçage axial, le perçage orbital est une autre façon de réaliser un trou cylindrique par enlèvement de copeaux. C’est une combinaison de deux mouvements de rotation qui utilise, non pas un foret, mais une fraise. Ce procédé d’usinage de trous présente de nombreux avantages mais, à ce jour, il est encore peu répandu dans l’industrie aéronautique, notamment parce qu’il génère un niveau plus faible de contraintes résiduelles dans les matériaux.”
“Il s’agit là d’un aspect crucial de la fabrication d’une aérostructure. Durant son exploitation, l’avion est soumis à de nombreux cycles de décollages, vols et atterrissage lors desquels il subit des variations importantes de pression et de température. Ces contraintes ont un impact direct sur la fatigue de sa structure. Celle-ci étant assemblée par rivets, il est nécessaire de garantir un certain niveau de contraintes résiduelles dans les trous qui les accueillent.”
“Avec un perçage classique ça se passe bien mais, pour le perçage orbital, le point d’interrogation c’est justement sur cette propriété physique de la matière après perçage. A priori, celle-ci présente moins de résistance mécanique que dans le cas d’un perçage au foret. Le premier axe de travail du projet RODEO a donc consisté à proposer et évaluer un procédé original de perçage et brunissage orbital qui permette de garantir les niveaux requis de tenue en fatigue des assemblages percés-rivetés.”
“Le deuxième enjeu était de mettre en œuvre ce procédé sur un moyen robotisé léger. Ce type d’intégration correspond en effet aux attentes actuelles du secteur de l’assemblage aéronautique, en recherche de solutions flexibles et performantes. La difficulté résidait ici dans le fait d’associer un procédé qui génère un effort radial tournant à haute fréquence avec un bras robotisé qui présente une certaine souplesse, le tout, en respectant des tolérances d’usinage de l’ordre de 50 µm.”
“Le rôle de MITIS n’était pas de développer le procédé de perçage orbital en tant que tel, mais d’évaluer les capacités de ce procédé par la mesure physique et l’analyse de signaux pour définir les meilleurs paramètres de fonctionnement au regard du cahier des charges défini. Et c’est précisément un domaine d’expertise développé depuis 12 ans chez MITIS, notamment à travers le déploiement de notre procédé de Perçage Vibratoire.”
L’intervention du LS2N, laboratoire des sciences du numérique de Nantes
Mathieu Ritou, Maître de conférences au LS2N (Laboratoire des Sciences du Numérique de Nantes) et à l’IUT de Nantes :
“Le rôle de PRECISE, KUKA Aerospace et du LS2N était le développement de la tête orbitale ORBIBOT et de la cellule robotisée de perçage orbital, avec un cobot IIWA. Ensuite, nous avons réalisé des essais de perçage instrumentés sur la cellule de perçage orbital robotisé pour déterminer sa capabilité. »
« Avec l’Institut Clément Ader et la thèse de Landry Kamgaing, nous avons étudié l’impact du perçage orbital sur les contraintes résiduelles et la tenue en fatigue de l’assemblage. Contrairement à certains a priori dans le domaine aéronautique, nous avons prouvé qu’il n’y a pas d’abattement de la tenue en fatigue en perçage orbital (en comparaison du perçage axial) ; et ce d’autant plus après boulonnage des éprouvettes percées [1]. C’est un résultat industriel très important. En effet, comme perçage orbital génère bien moins d’efforts, cette technologie est donc davantage adaptée pour la robotisation. »
« Le topic manager Suédois, SAAB Aerospace, est très satisfait des résultats du projet. Il nous a proposé d’aller au-delà et d’effectuer une démonstration dans un projet plus ambitieux. SAAB est en charge de concevoir des portes d’avions innovantes et ils ont souhaité que le consortium réalise du perçage orbital robotisé pour l’assemblage de l’une de ces portes. Celle-ci sera exposée lors de la présentation finale des résultats du grand programme aéronautique européen CleanSky2 à Hambourg en 2021. »
« L’accompagnement de la Cellule Europe du Pôle EMC2 et de l’Université de Nantes nous a beaucoup aidé à aller vers des projets européens tels que celui-ci.”
[1] Kamgaing, L., Landon, Y., Senatore, J., Daidie, A., Ritou, M., « High Speed Orbital Drilling Optimization and Fatigue Life Enhancement by Orbital Roller Burnishing for Aluminum Alloy » SAE Int. J. Adv. & Curr. Prac. in Mobility 2(2):774-786, 2020